Dedicated to excellence and innovation in sluice room products
DDC was founded with the purpose of safeguarding vulnerable patients, care home residents and front-line clinicians from the risk of infectious diseases through engineering innovation.
Since 1991 we have designed, engineered and continually developed sluice room machinery, including bedpan washer disinfectors, medical pulp macerators and incontinence product macerators
We manufacture all our sluice room equipment at our UK headquarters based in Poole, Dorset, and export our products all over the world; providing a one-stop-shop for all your sluice room requirements.
For almost 30 years the DDC team have been dedicated to excellence and innovation in sluice room products, service and maintenance in the UK and around the world.
1991 - DDC Ltd Established
DDC was founded - dedicated to excellence and innovation in sluice room products and solutions.1992 - Products
Panamatic range of bedpan washer disinfectors launched. New innovation and technology to significantly reduce healthcare associated infections.1998 - Incomatic launched
Incomatic nappy pad macerator launched.2001 - Services
Expanded into machine service and maintenance to provide better support to customers and increase the lifespan of our products.2006 - Introduced HTM 2030
Introduced HTM 2030 testing service for hospitals, adding increased value and services to key customers.2007 - Developed Pulpmatic
Developed Pulpmatic range of macerators. Now able to service all sluice room needs for greater convenience to customers.2018 - Launched 360° Care Cover
Launched 360° Care Cover packages to help customers spread the cost of financing a new machine alongside ongoing care and maintenance.2019 - Launched 360° Service
Launched 360° Service regular maintenance packages to help customers keep their sluice room machinery in excellent operational health.2019 - Launched 360° Chemical
Launched 360° Chemical packages so that customers always have sufficient chemicals for their facility’s requirements, delivered at a frequency to suit them.2019 - Developed the UVMATIC Air Purification System
Developed the UVMATIC Air Purification System to assist hospitals and care homes with eliminating odour and reducing harmful airborne bacteria.2019 - UK's first range of eco-friendly personal hygiene and cleaning wipes
Developed the UK's first range of eco-friendly personal hygiene and cleaning wipes – 100% maceratable, flushable, dispersible, biodegradable and compostable.2020 - Launched the Pulpmatic Eco+
Launched the Pulpmatic Eco+ medical pulp macerator - the most economical and eco-friendly sluice machine on the market.2021 - Hygenex
Launched the Hygenex brand and website focused on medical-grade sanitation solutions.2021 - 30 Years!
Celebrated our 30th year of infection control excellence and innovation.2021 - Vacumatic Waste Disposal
DDC launch new Vacumatic Waste Disposal product, complete with airtight sealing for enhanced infection control.2022 - Relocation
DDC relocated to a new purpose-built facility providing greater energy efficiency.2023 - revamped Panamatic product range
DDC launch a revamped Panamatic product range, delivering cutting edge efficiency and enhanced infection control.2025 - Launch Pulpmatic Flex
DDC unveils the Pulpmatic Flex at Arab Health
2025 - Launch UVC range
At Arab Health 2025, DDC unveiled the new UVMATIC range, featuring the MultiTower, AirSafe, WaterTrap, PureAir, and PureAir+.
DDC design, innovation and manufacturing excellence prevents infection – safeguarding vulnerable patients, care home residents and frontline clinicians in hospitals and care facilities around the world.
To reduce global infection rates by delivering an inspirational range of products, backed by world-class technical expertise and exceptional service.
We drive innovation by investing in future development to anticipate evolving healthcare demands.
We are committed to continual engineering innovation to meet ever-changing customer requirements, helping them to achieve excellence.
We are defined by our integrity and will respectfully question, challenge and listen to our customers’ needs.
We are dedicated to building a great workplace where all can thrive.
We believe that by working together anything is possible.
Corporate Social Responsibility
DDC is committed to reducing its impact on the environment by driving innovation, improving supply chain resilience, and evolving to support a lower carbon economy.
Our pledge is underpinned by:
- Environmental action which increases energy efficiency, reduces waste, prevents contamination of natural resources and shrinks the carbon footprint throughout our operation
- Employee engagement which encourages personal commitment to sustainability objectives, within our company and beyond
- Evidence of achievement by measuring our progress against fixed goals.
Through this work, we strive to improve global health – in hospitals, in care homes and in the world around us.
Here’s what we look for in a strategic partner
Accreditations
DDC is proud to be acknowledged for our quality and expertise by the following bodies
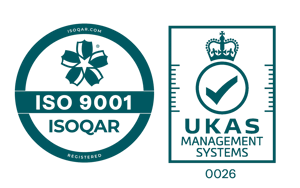
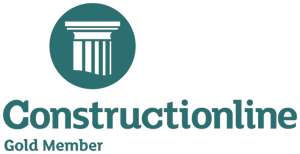
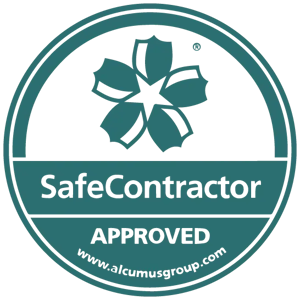
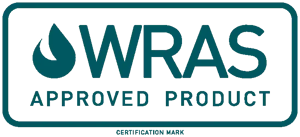
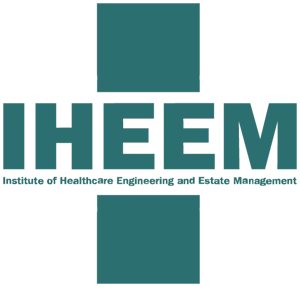
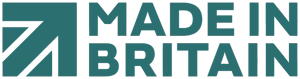
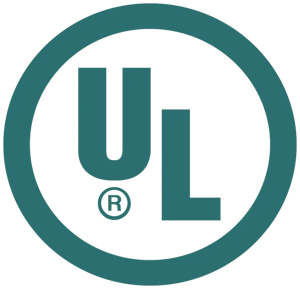
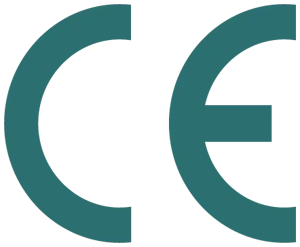
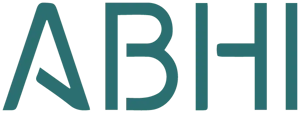
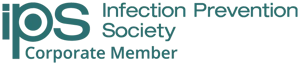
10 Reasons You Need DDC Infection Control Technology For Your Hospitals Or Care Homes
- Improve safety for hospital patients, care home residents, clinicians and carers, improve patients’ and residents’ dignity.
- Reduce the risk of inter-patient/resident/staff HCAI infection
- Reduce the risk of infection transmission following contact with surfaces
- Reduce airborne infections, remove bad odours.
Every year, hundreds of thousands of patients contract Healthcare-associated Infections (HCAIs) while being cared for in NHS hospitals.
Hospitals and care homes around the world depend on DDC leading-edge infection-control solutions to stop the spread of HCAIs – saving lives, preventing injuries, reducing treatment/rehabilitation times and improving outcomes.
World-class infection-control technology from DDC includes:
- Medical pulp macerators – advanced anti-infection features include hands-free operation and antimicrobial surfaces. View the range…
- Bedpan washer disinfectors – dispose of hazardous human waste quickly, effectively and more safely than traditional hand-washing methods. View the range…
- Incontinence product macerators – dispose of incontinence pads and nappies in a safe, fast two-minute cycle, freeing up more time for hands-on care.
- Hygenex Vacumatic waste disposal system – 100% hygienic, efficient and odourless waste disposal without the risks associated with traditional yellow bags.
- Advanced UVMATIC® and UVMATIC ® Plus UV air purifiers that combine photoplasma, ozone and negative ions to destroy viruses (such as influenza), bacteria (including E.coli, salmonella) and mould.
- Hygenex Recoat antimicrobial coating system – protect surfaces from HCAIs including E. coli, MRSA, Staph aureus and SARS-CoV-2.
- Maceratable, compostable, flushable, biodegradable wipes (wet or dry) made from 100% natural materials – fully compliant with EDANA and INDA flushability standards.
- Solve existing issues that affect your CQC rating.
- Improve your CQC rating.
- Improve patient outcomes at your hospital – avoid CQC enforcement action.
- Improve care at your care home – make it first choice, increase revenue, profits and margins.
CQC inspections can make or break the reputation of your hospitals or care homes.
The Care Quality Commission has the power to issue requirement notices, warning notices, cautions and fines, impose conditions, place providers in special measures – and prosecute cases where people have been harmed or placed in danger of harm.
Learn how to avoid an ‘Inadequate’ CQC rating at your care home. Read more…
How to meet the latest criteria for care home CQC inspections. Read more…
Get help with CQC compliance...
All DDC Dolphin’s advanced medical pulp macerators save time by reducing the need to clean reusable items. They are economical, saving energy and water – reducing operating costs, and preventing ward shutdowns due to infection.
- Pulpmatic Ultima macerators can pulp up to six items in each 120-second cycle.
- Pulpmatic Uno pulps one or two items in each 65-second cycle – with low noise, ideal for small wards and care homes.
- Pulpmatic Eco+ is the most economical and environmentally friendly machine on the market – processing up to four items per cycle (lasting from 85 seconds).
And the Hygenex Vacumatic waste disposal system cuts costs by vacuum-compacting and sealing waste – reducing storage, collection and disposal costs. Waste volume is reduced by 50%.
Waste is vacuum-sealed 100% hygienically. Odours, viruses and bacteria are filtered out through a validated 0.2 micron filter.
Each Vacumatic unit can be wheeled quickly and easily from ward to ward or room to room – supporting your sluice room operations or providing an efficient alternative to maceration.
Reduce the cost of sluice room operations. DDC’s advanced medical pulp macerators, bedpan washer disinfectors and incontinence product macerators are designed to use less energy and water.
This has never been more important with the rising cost of energy and the critical importance of reducing your carbon footprint to meet environmental targets for NHS facilities and their suppliers.
Properly serviced and well maintained sluice room machines last longer – reducing the financial and environmental cost replacing them.
DDC’s 360° Care, 360° Service and 360° Chemical contract packages reduce the costs and administration associated with your sluice rooms.
- Cost-efficient, dependable sluice room equipment. 360° Care includes a five-year parts and labour warranty, service and maintenance visits over five years, chemical supply, machine installation and commissioning, carriage and packaging, a pre-installation site survey and sluice room health check. Find out more
- Superior aftercare. 360° Service includes annual or twice-yearly service maintenance visits, parts and labour warranty, discounts on chemicals and parts, SLA response times, a sluice room health check, water hardness and scale level checks (with recommendations), annual account review, annual periodic testing to NHS guidelines. Find out more…
- Up to 15% discount on chemicals. 360° Chemical maximises efficiency – giving you regular deliveries of chemicals at a frequency to suit you: right amount, right time – based on usage forecasts. Get between 5% and 15% discount on your chemical order if you have a 360° Service contract. Find out more…
- Save time and money on servicing and maintenance. DDC is the only company able to service all makes and models of sluice machines, so you don’t have to call in different engineers for different machines. This ‘whole-of-market’ technical expertise and experience saves time (benefiting patients and residents), reduces call out charges and so lowers your repair bills. Find out more…
Our UK-wide network of service engineers implements Covid safety protocols to ensure your patients, clinicians, care home residents and carers remain safe and protected at all times during maintenance and inspection visits.
Engineers can carry out work in full hazmat suits – not just basic PPE – for maximum infection-control protection. They are used to working in hospitals that treat patients suffering from highly infectious tropical diseases – contagions that are far more deadly than coronavirus.
Find out more about how DDC can help you:
- Cost-Saving Ideas For Hospital Sluice Rooms. Read more…
- Reduce The Cost Of Running Your Care Home With Reliable Sluice Room Consumables. Read more…
With 30 years’ experience, DDC provides strategic, holistic turnkey solutions that meet your full infection-control requirements – not just for your sluice room, but for the entire estate in your healthcare trust or portfolio of care homes in your group.
One expert and specialist single-source supplier can:
- Health check your hospitals and care homes to help you determine your infection-control requirements across your entire trust or group. Not just for sluice rooms – DDC Dolphin can also recommend and provide antimicrobial surface protection, air purification solutions and staff training for every ward, unit, hospital or care home.
- Advise you on the best way to integrate DDC’s new and more advanced infection-control technology with your existing equipment – seamlessly, efficiently, cost-effectively and with minimum disruption to your operations.
- Help you to procure machines, consumables and servicing in the most efficient way:
- reducing administration costs
- complying with your specific requirements and procurement best practice
- suggesting opportunities to enhance and streamline procurement. - Deliver superior aftercare in the most cost-efficient way to help you extend the life of all your sluice room equipment – not just DDC machines.
Find out more about infection control for:
HCAIs endanger patients and delay their discharge from hospital. This in turn impacts on other patients needing treatment. Waiting lists grow as wards are closed for deep cleaning.
Infection outbreaks disrupt the smooth running of hospitals and place added demands on staff – not just on frontline clinicians but also on administrative staff who have to rearrange appointments following the postponement of surgery and other procedures.
Waiting times are already growing due to the impact of the Covid-19 pandemic. British Medical Association data for September 2015 to December 2021 puts the NHS waiting list at more than 6.00 million – compared with 4.43 million in February 2020.
The total number of patients waiting more than 18 weeks for treatment now stands at more than two million. Some 310,000 patients have been waiting for a year or longer.
HCAI outbreaks undermine all the work needed to reduce this backlog – work being carried out by beleaguered staff exhausted by the added pressure of coping with treating patients infected with Covid-19.
Care
Patient care and well-being is at the heart of every DDC innovation. Specify advanced sluice room equipment that speeds up the safe and hygienic disposal of human waste.
Good infection control should not mean having to sacrifice time at the expense of other important aspects of patient engagement. It should not be a dilemma or a balancing act – not if you use the right technology: high-performance sluice machines that save time as well as money and the environment.
The less time your clinicians and carers have to spend operating macerators and bedpan washer disinfectors, the more time they can spend with patients and residents.
Find out more about infection-control solutions that give time back to care.
“The definition of genius is taking the complex and making it simple.” Albert Einstein.
Every machine in your sluice room should be easy to operate. Controls must be intuitive and internationally recognisable to avoid any confusion. Errors in health and social care environments can spread infection – so our machine designers have worked to eliminate them.
All the hands-free controls on our macerators are simple and hygienic:
- open the macerator by placing your foot in the foot cup
- place the pulp and its contents in the machine
- close the lid and start the cycle by either placing your foot in the foot cup again or by placing your hand in front of a touch-free optical sensor.
Ensure all your staff implement infection-control best practice. Find out more here about Continuing Professional Development (CPD) courses – keep up to date with the latest developments and technologies.
CPD courses can be delivered either virtually or on-site.
Medical Negligence Claims
Failure to deal with infections inevitably leads to costly medical negligence claims against NHS trusts.
Every year, Sepsis (the body’s extreme reaction to infection) claims 31,000 lives and costs NHS England around £2 billion per year. The government estimates that 11,000 lives and £160 million could be saved every year through better diagnosis and treatment.
But prevention is better than cure. Eliminate the infections that lead to sepsis by strengthening infection-control procedures. Defending claims and paying damages to litigants far exceeds the cost of investing in superior infection-control technology.
The amount paid out in NHS medical negligence claims in 2020/2021 fell by £120 million, according to NHS Resolution, the “arm's-length body” of the Department of Health and Social Care that helps the NHS to resolve disputes fairly. One of the factors cited for the fall was that “the process of investigating and resolving claims slowed somewhat during the pandemic.”
But the NHS has struggled to cope with infection control during the pandemic.
One-in-seven patients treated for Covid-19 between 1 August 2020 and 21 March 2021 caught it while being treated in hospital for something else. (Source: NHS England data).
Suspected Covid-19 outbreaks in UK hospitals doubled in the seven days to 16 December 2021 – from 33 to 66, (Guardian newspaper report, based on official data).
In May 2020, NHS England data revealed that 32,307 patients had probably or definitely contracted Covid while in hospital since March 2020 – 8,747 of them died.
Four per cent of all UK greenhouse gas emissions are down to the NHS, significantly less than transport (27%), energy supply (21%) and business (17%) – but still a major cause for concern and action.
The NHS has committed to becoming the world’s first zero carbon national health service – net zero emissions by 2040 (with an 80% reduction by 2028-2032).
And the NHS Carbon Footprint Plus target cascades the requirement down through the supply chain. Suppliers must be net zero by 2045 (with an 80% reduction by 2036-2039).
Specify DDC and Hygenex solutions to improve infection control and reduce your carbon footprint:
- Pulpmatic medical pulp macerators – energy-efficient, water-saving, high-performance macerators. They are manufactured in the UK, reducing the impact of shipping/transportation on the environment. View the range…
- Panamatic bedpan washer disinfectors – advanced temperature control means minimal waste due to efficient use of power and water. View the range…
- Hygenex fully biodegradable wipes – unlike other supposedly ‘flushable’ wipes, they are manufactured from 100% natural materials and contain no microplastics. Find out more, watch the 64-second video…