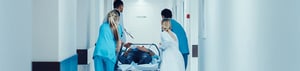
10 Golden Rules For How To Keep Your Bedpan Washer In Good Working Order
Whether you work in a hospital, care or nursing home, hospice, or a special school, if you have a bedpan washer, your staff need to know how to use it – and use it correctly.
Unfortunately, it’s often the case that not everyone is trained to the same standards. This is when problems can arise from incorrect operation.
That’s why we’ve put together our 10 golden rules for proper bedpan washer usage, to help all staff understand what they need to do to keep their machine in good working order.
Rule 1: Know your machine
Every model is unique, so it’s important to know exactly what your machine is capable of.
You need to be aware of the maximum load capacity of your machine to ensure a thorough disinfection cycle. It’s also important to know how your bedpan washer has been programmed – for example, if you have an automatically closing lid, so that you don’t manually force the lid shut.
Rule 2: Train your staff
It might seem like an obvious point, but it’s probably the most important – your staff need to be trained how to use your machine. Our experience shows that the most common cause of bedpan washer breakdowns is user error.
The DDC website is a good place to start if your staff have any questions about your specific machine.
We also offer training to your clinicians and care staff for best practice operational procedures and infection control when operating in a sluice/dirty utility room environment. We can do this as a one off or on a regular basis as part of a 360° Service contract
Rule 3: Regularly clean the outer surfaces of the machine
Even if you are meticulous with your infection control procedures in your sluice room, it’s all but impossible to prevent harmful microbes from getting into the air and settling onto both the machinery and nearby surfaces, clothes and skin.
Our most advanced machines come with antimicrobial coatings and smooth, crevice-free surfaces to prevent the growth of harmful bacteria.
You should clean the outer surfaces of the bedpan washer, including the lid/door and seals at least once a day with a mild, non-abrasive detergent to remove any residual microbes which may have settled on the surfaces during the day.
You should always use approved cleaning products to keep your bedpan washer clean and fault free. DDC’s Hygenex range meets or exceeds current government guidelines on clinical safety standards to help prevents the spread of infectious diseases.
Rule 4: Don’t overload the machine
Our bedpan washers come with a range of load capacities to suit your facility, and various different load configurations to suit the type of utensils you use.
It is important to not put more utensils than advised in the machine and to stack them in the configuration advised to guarantee that your utensils will be properly disinfected.
Our bedpan washers have a combination of high pressure rotating wash nozzles and strategically sited spray jets to ensure superior wash performance. If you follow our advice on how to load the machine you can be assured that your utensils will be thoroughly disinfected.
Rule 5: Don’t put things inside which aren’t supposed to go there
A common cause of malfunction, blockage or breakdown is when users accidentally put things inside the machine which they aren’t supposed to– such as disposable gloves or aprons.
This should be a simple rule to remember – bedpans, commode pots and urine bottles, plus the human waste they contain are the only things that should be placed within a washer disinfector.
Rule 6: Don’t interrupt the wash cycle
Some manufacturers allow their wash cycles to be interrupted, for example if a user wanted to add an additional item to the wash, or they didn’t realise the machine was running.
However, it’s vitally important not to do this. If you stop the cycle halfway through or open and close the door, the water won’t be heated to the temperature required in order to kill or denature harmful microbes and your bedpans won’t be properly sanitised.
If you don’t let the wash run for the full length of the cycle, the waste itself may not even be properly removed from the surface.
An incomplete cycle could also result in waste build-up resulting in a blockage and overflow next time the machine is used.
DDC machines can only be interrupted by switching off the power during the wash cycle, so unless the cycle is intentionally interrupted, your bedpans will be fully disinfected.
Rule 7: Use approved cleaning chemicals during pre- and post-wash cleaning cycles
DDC washer disinfectors have the added feature of pre- and post-wash cleaning cycles.
This means that your drains are fed with a steady flow of water which helps to prevent blockages and avoid potentially problematic chemical and waste build up.
It’s important to use an approved chemical as there are only a handful that are legally permitted to be flushed down drains, as they need to be able to be removed during water treatment and not cause damage to drains.
DDC’s EcoWash+ meets current government guidelines on safety standards, helps the cleaning process, reduces limescale and deodorises the machine ready for the next user.
Rule 8: Use a scale management system
Limescale can present a real challenge in maintaining cleaning performance, especially if your hospital or care home is situated in a hard water area.
That’s why you should use a limescale inhibitor like our Scalematic to reduce the build-up of limescale throughout your machine.
It’s essential to prevent limescale accumulation as it won’t just clog your pipes, but it will form on any surface that water comes into contact with – including the heating filament. If this gets coated in limescale it will need to use more energy to heat the chamber to 80o Celsius and – if left untreated – the machine will eventually fail to achieve thermal disinfection.
Rule 9: Make sure your machine is tested and maintained to HTM2030 standards
In the UK, HTM 2030 is a document outlining correct methods and procedures for all types of washer disinfectors in the Acute Healthcare Sector. It lays out exactly what’s expected of us as manufacturers and you as operators in order to minimise the risk of infection during the disposal/disinfection process.
We put the guidance laid out in HTM 2030 at the heart of everything we do – it underpins our machine design, usability, performance and life expectancy.
But it’s also important for you as a user – it gives guidelines from how your sluice/dirty utility/pan room is designed to what you are supposed to do in the event of a breakdown.
If you fail to follow best practice, for example when reporting or attempting to fix a malfunction which then results in an outbreak, there could be serious consequences.
Rule 10: Schedule planned preventative maintenance
No machine is impervious to component failure or simple happenstance – that’s why we recommend 360° Service to spot the failure before it happens.
It prevents leaks, build-up of limescale or hazardous residue, and greatly reduces the likelihood of a blockage or breakdown.
Not only will this save you the expense of unexpected engineer callouts and repairs, but it will keep your sluice room fully operational and reduce down time, increase the lifespan of your machine, and keep your clinicians, care workers, patients and service users safe.
We offer training to your clinicians and care staff for best practice operational procedures and infection control when operating in a sluice/dirty utility room environment. If you need any help with ensuring your staff are fully trained on how to operate your washer disinfector, get in touch today.