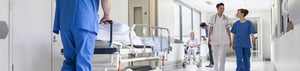
How to Stay Compliant with Sluice Room Legislation
Ensuring that your sluice room is fit for purpose, as well as meeting the relevant legislation, starts right from the concept stage.
Healthcare acquired infections (HCAIs) are an ever-present threat in medical facilities. For as long as this is the case (and, realistically, we’re unlikely to experience a future without bacteria), infection control must be kept front of mind.
When the CQC inspectors come to call, they’ll be looking for evidence of your compliance in a number of areas – and this includes your sluice room management. In order to assess how you measure up, they’ll use the Health and Social Care Act 2008 (Regulated Activities) Regulations 2014 – Regulation 15 as a guide.
The intention of this regulation is to make sure that your care and treatment premises are clean, as well as suitable for the intended purpose.
This includes – but is not limited to – making sure that individual facilities are well-maintained, clean and appropriately located. In addition, the equipment used to deliver care (such as bedpans and commodes) must be kept sanitary.
Health Building Note 00-09: Infection Control In The Built Environment provides guidance for all providers of NHS care to ensure that estate requirements are met.
Discussing the various stages of a capital build from start to finish, HBN 00-09 will help you to ensure that your sluice room can do its job efficiently – from the ground up.
The information outlined in the document leans on the general principles given in the ‘The Health and Social Care Act 2008: Code of Practice on the prevention and control of infections and related guidance’ (the HCAI Code of Practice).
Underlining major infection prevention and control (IPC) issues, HBN 00-09 will help you to offset future HCAI concerns, by making sure that risk reduction is ‘built in’ from the start.
Assisting designers, architects, engineers, facilities managers and planners to work in unison with IPC teams, healthcare staff and service users, the initial work is part of a long-term strategy.
Although HBN 00-09 doesn’t cover operational management of IPC (such as managing outbreaks of infection) or everyday precautions, it will put you in good stead to action your individual infection control procedures, in the knowledge that your sluice room is ready for action.
Infection Prevention and Control is triggered throughout the design and build process.
With specific measures in each key area, opportunities for HCAIs to develop are prevented, at every stage
At this initial stage, IPC should immediately come into practice, with consideration paid to the impact of design on space/sizing, decontamination and specialist areas.
2. Sketch Plans
When plans are being sketched, you will need to assess if the design can support suitable infection control precautions. This would include storage (linen, waste, patient equipment, cleaners’ equipment), ancillary areas, changing facilities (if required) and the location of hand hygiene facilities.
3. Detail Planning/Design
At this stage, it’s time to discuss the final details of the facility’s location, as well as the type of fixtures and fittings; equipment schedules, wastewater and sanitation provisions will all come into play.
4. Contract
Have you considered the control of legionella and aspergillus on the wider plan? You will now…
5. Monitoring/Construction
Issues to consider during the monitoring and construction process include any alteration to the agreed design, as well as IPC risk and control measures (fungal spores, etc).
6. Pre-Handover Inspection/Commissioning and Equipment/Post-Project Evaluation
This will be the final opportunity to inspect, test and demonstrate compliance with IPC, before the facility is opened for use.
There are examples of design principles that you should also follow, in order to ensure that your sluice room is compliant.
When following these principles, you should consider:
1. Does the design facilitate cleanliness and cleaning?
In order to keep your sluice room sanitary, you should ensure that finishes that are impervious, smooth and seamless, as far as practicable; stainless steel is a good choice. You should also consider the hands-free operation of utilities.
2. Are you encouraging desired behaviour (such as hand hygiene)?
This could involve providing sufficient space for activities to avoid cross-contamination; ensuring proper segregation and management of waste; providing enough hand-wash basins and antimicrobial hand-rub dispensers; suitable facilitates for the cleaning of equipment, and a plan to deliver good separation of clean and dirty jobs.
3. Have you designed for easy cleaning?
It’s always best to maintain a visibly clean environment, but this is absolutely critical in the sluice room environment. Good facility design will make this much easier, by providing finishes that are easy to clean.
Although there may be a pressure to choose the cheapest as opposed to the best, you should always pay attention to whole-life costs. Will the expense of cleaning and maintaining an inferior product put a long-term strain on your budget?
HBN 00-09 provides specific guidance for ancillary areas, such as your sluice room.
The recommendation from the Health Building Note is to ensure that your dirty utility room supports the following:
- Testing urine
- The disposal of body fluids including water contaminated with body fluids, exudate, etc.
- The decontamination of commodes
- Temporary holding of items requiring reprocessing
- Clinical handwash facilities
- Clear demarcation between clean/unused equipment and solid/dirty equipment
- Separation of clean and dirty areas, with a clearly defined workflow pattern.
Bedpan washer disinfectors and macerators are subject to specific recommendations, too.
HBN 00-09 advises the following:
- Washer disinfectors are to comply with Choice Framework for local Policy and Procedures 01-01 Part D – ‘Management and decontamination of surgical instruments: washer-disinfectors’. Hands-free door opening machines are recommended.
- Where fitted, bedpan washer disinfectors should be installed according to the Water Supply (Water Fittings) Regulations 1999 to prevent backflow and contamination. Easy access is essential.
- One should always confirm that internal drains and external sewerage systems can cope with the slurry from macerators.
- Where reusable supports are used with medical pulp products, there should be adequate facilities to ensure they are cleaned between users.
It’s a lot to consider, but with the right support and preparation, your overall facility will benefit from the efficiency of your sluice room.
DDC provide the full spectrum of sluice room guidance – from the initial design of your facility, to the financing of sluice room equipment and ensuring that you are equipped with a reliable service and maintenance package.