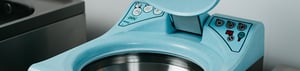
Improving Infection Control at an International Scale
Infection is a threat which infiltrates every inch of the globe.
At DDC, we’re leveraging the latest healthcare technology to improve infection prevention and enhance patient outcomes around the world.
DDC have been providing excellence and innovation in the infection control market for over 30 years. From industry-leading sluice room equipment to unmatched service and maintenance provisions, we are immensely proud of how many facilities have vastly improved their infection control standards with our help.
Since our inception in the UK in 1991, we can now be found in over 5000 facilities in 50 countries on 6 continents – all while maintaining the same quick, efficient, and personal service levels of a local supplier.Furthermore, we are pleased to report that we have doubled export sales (+104%) year on year, in the last 12 months.
DDC exports a range of unique infection prevention solutions to healthcare facilities across the world. The key products that we export are pulp macerators, washer disinfectors, air purification units, pulp disposables, disinfectant wipes and eco-friendly patient care wipes.
DDC has been at the forefront of innovation in the global healthcare sector for over 30 years, developing unique products with value added features - such as contactless operation and antimicrobial coatings.
More recently, with the global focus on sustainability, DDC has developed a range of medical-grade, innovative eco-friendly patient care wipes which are plastic free and sustainable.
What is DDC’s strategy for growth through international trade?
We are set apart by our ability to deliver a full-service solution for our international partners – spanning from sluice room equipment (such as pulp macerators and bedpan washers) to infection control guidance and water management, supported by complementary products and consumables.
Our sluice room equipment is designed, tested, and manufactured in the UK, but we supply hospitals and care homes all over the world. We work with 30 distributors who are strategically positioned around the globe, helping over 50 separate markets and over 800 facilities to implement the most appropriate sluice room solution.
A single point of contact gives DDC a unique one-stop-shop methodology to sluice room planning and design. Whether a new facility is being built or an existing site is being upgraded, DDC can assist with every stage of the design, build and procurement process, ensuring that hospitals and care homes benefit from optimised space, innovation and architecture, centered around their specific needs.
We provide everything required for a well-managed sluice room inventory. This includes supplying our own range of consumables to complement DDC machinery, and avoid the maintenance issues that can occur from non-compatible products. This emphasis on a full-service solution empowers our partners to maximise their assets, which creates long-term value – as well as propelling our own growth, through expanding international trade.
How is DDC increasing sales through exporting?
DDC has seen a significant rise in export sales over the past 5 years, successfully achieving 150% growth over a 5-year period. This has enabled DDC to create more jobs in front and back-office functions and provide career development opportunities for members of the team.
Exporting has also improved DDC’s business as it has re-invested profits back into the organisation to help fund research and development for new product innovation. The company has recently launched its next generation of pulp macerator, the Eco+, which is the most hygienic and environmentally friendly product available on the market
Which new markets have DDC accessed?
We’ve helped over 50 separate markets and over 800 facilities to implement the most appropriate sluice room solution. This includes significant growth specifically from developing markets like Latin America (Chile, Mexico), Europe (Holland, Norway, Poland, Ireland) and the East (Qatar, Japan, Singapore, Australia).
Our ability to reach healthcare facilities around the world is underpinned by long-standing relationships with trusted distributors, who are strategically positioned across the globe.
By building business through well-established partnerships, we can grow at pace in critical international markets – allowing us to tap into all-new worldwide opportunities, while also creating excellent results for customers.
What challenges have DDC faced and overcome?
Exporting has enabled DDC to expose its products to a global audience. This has encouraged some excellent feedback, leading to product innovation.
For example, a customer in Canada was facing some challenges in training people how to use our equipment due to the fact they had not experienced the technology before. To overcome this, DDC’s innovation team developed an audio instruction system and graphic user interface which provides product training at the point of use. This technology feature is now suppled to all customers in Canada and has added significant value to the users of the equipment.
The outbreak of the pandemic in 2019 presented exponential challenges in our market, but DDC was on hand to support many organisations around the world in the fight against COVID-19. Due to our market position within infection prevention and hygiene, we helped thousands of healthcare facilities across the world during a crucial time.
Although running a business through this time was extremely difficult, it enabled
DDC to review internal and external processes, and become a better business moving forwards.
What is DDC’s plan for sustained growth in international markets?
DDC believes that exporting is crucial to our future business growth and development plans. We have an ambitious vision for the future and have just moved into a new facility, which will enable the company to expand its manufacturing capabilities. This will also enable the company to create new manufacturing and office-based roles.
DDC is proud to be at the forefront of innovation within our sector. We are committed to developing an inspirational range of products that support healthcare workers in their day-to-day operations and contribute to their infection prevention and control strategies.
DDC is also working on a next generation of macerators and washer disinfectors, which the company plans to launch in 2023 and 2024. We are very excited to bring our latest innovations to our UK and export customers.
Our latest innovations have carefully considered sustainability objectives, which will be at the heart of our product design moving forwards.
DDC is in the process of entering the US market and we expect further developments on this exciting market in 2023 and 2024.
How is DDC enhancing its products, services and processes to enable exporting?
DDC is unique in the fact that we are the only global company to manufacture both pulp macerators and washer disinfectors, which are used in healthcare facilities as part of their patient care infection control strategy.
Pulp macerators, pulp disposables and eco-friendly patient care wipes are a single use solution to patient hygiene concerns in healthcare facilities across the world. In a single-use strategy, healthcare patients or care home residents are provided with a pulp disposable for tasks such as patient toileting, patient bathing or administration of care. The used pulp disposable and its contents are then disposed of in a pulp macerator.
The single use system provides a high level of hygiene and infection prevention and offers a sustainable solution to patient care, as pulp disposables are made from recycled materials that are FSC certified. Our eco-friendly patient care wipes, for example, are EDANA certified and meet the 7 global standards for “flushability”.
DDC is currently delivering a project in Mexico via one of our distribution partners to equip a significant number of healthcare facilities with this single use system. It has been proven to improve nurse productivity and patient care, as well as contributing to improved infection prevention and control.
However, re-usable products are also important to global infection control strategies. In a re-usable system, healthcare patients or care home residents are provided with a reusable plastic or steel receptacle for tasks such as patient toileting, patient bathing or administration of care. The used receptacle and its contents are then disposed of in a washer disinfector.
DDC is currently delivering a re-usable system project to a facility in Poland, via one of our distribution partners. This will no doubt improve on their current infection control procedure and lead to greater healthcare outcomes.
Global Infection Control in Action: Working with Our Distributors to Support Juntendo University Hospital in Nerima, Japan.
Juntendo Hospital was the first private hospital in Japan, originally founded in 1838 as a Dutch School of Medicine at a time when Western medical education was not yet embedded as a normal part of Japanese society.
The Infection Control Team at Juntendo had found several used bedpans in the sluice room, waiting to be washed - resulting in a very unhygienic working environment for staff. This was caused by busy wards and staff that could not wait for the bedpan washer to complete its cycle.
To reduce exposure to staff working in the sluice room and improve the sluice room environment, the Infection Control Team began to consider switching to single use pulp products. While working with Sakura – one of DDC’s global partners - a Pulpmatic Ultima medical pulp macerator was introduced in the Emergency Department, for a 6-month trial period.
After a successful trial period, Sakura were instructed to install a further 11 Pulpmatic Ultima and Pulpmatic Uno macerators. The DDC macerators and single use pulp not only reduced the risk of cross contamination, but it also provided a much-improved sluice room environment.
“Apart from the operational benefits, switching to medical pulp macerators greatly improved the sluice room environment and the cooperation between the Infection Control Team and ward staff. We were very impressed with the overall benefits of using this system and the future for us will certainly be using macerators and single use pulp wherever possible.” - Mr Tomohiko Iizuka, ICN - Juntendo University Nerima Hospital.