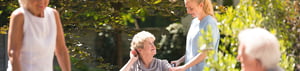
How To Prepare Your Care Home For A CQC Inspection
A surprise visit to your Care Home from the Care Quality Commission can seem daunting, but it needn’t be.
Keep your staff prepared and it can be a great opportunity to demonstrate the excellence of your facility, including its infection control procedures. Visiting services is a vital part of the Care Quality Commission’s work.
As the independent regulator of health and social care in England, the CQC play an important role in ensuring the standards of healthcare institutions are kept high. The judgement of each inspection is made available to both the institution and the public, so the institution knows where it needs to improve (or celebrate, if it’s an Outstanding rating across the board), while the public are kept aware of the measure of their local facilities.
Most importantly, the CQC aim to ensure that those receiving care have the most effective, dignified and responsibly-managed experience.
When the CQC visit a care facility it gives them an opportunity to talk to both staff and service users, while also observing care and inspecting records to see how the needs of patients are managed. Most adult social care services can anticipate an inspection at least annually, so it makes sense to be continuously prepared; a CQC visit may be unannounced, but with your own pre-planning throughout the year, it needn’t be a nasty surprise.
A Care Quality Commission inspection will focus on five key areas.
Those assessing your care facility will want to know:
- Are you effective?
- Are you caring?
- Are you responsive to people’s needs?
- Is your facility well-led?
- Is your facility safe?
As part of the CQC’s inspection into your safety standards, they will expect to see appropriate infection control measures which are proportionate to the type of care your service users receive. Inspections are geared towards spotting non-compliance, but where compliance is seen, it’s used to provide a balanced report of your practices.
Specifically, the inspectors will want to see that premises are kept hygienically clean to guard against the spread of infection, with staff understanding their personal responsibilities. In addition, you should be able to demonstrate that policies and procedures regarding infection control are being maintained and followed in accordance to national guidance.
The easiest way to prepare for Care Quality Commission inspection is to ensure that standards in your facility are always high, every day, for every patient.
If your Care Home is consistent in its good practice, you’re very unlikely to be caught out on the day of the inspection; it’ll be just like any other day.
Using the most effective infection control machinery to suit your needs is a good place to start.
Investing in macerators to dispose of incontinence and pulp toileting products will prevent risky methods of waste collection; rather than putting products in a bin (which will no doubt become a hotbed for bacteria, let alone being messy and smelling unpleasant), a macerator will pulverise pulp products into fine particles, which are then flushed through the sewerage system.
Similarly, if your Care Home relies on the circulation of re-usable bedpans, washing by hand is a perilous exercise which can routinely expose staff and patients to infection. Using a washer disinfector is a far more effective method, which gives you the reassurance that your bedpans are being cleaned at the optimum temperature for sanitation, without anyone needing to get their hands dirty.
With many DDCmachines featuring hansds free technology and antibacterial coatings, your staff will be able to easily use macerators and washer disinfectors without risk of cross-infection from patient care.
In addition, if your facility is bound by a very tight budget, DDC can also offer a Technology Financing Solution to give you the flexibility of spreading the cost over a 2 to 5-year lease, as opposed to buying machinery outright.
Where macerators and washer disinfectors are in use, its also essential to stay stocked up on the relevant consumables (such as Hygenex EcoCleanse+ and EcoWash+ chemicals), which will ensure your machinery works at optimal efficiency.
Running low on the day of an inspection would be extremely disruptive; the same can be said of any disposable pulp products that you use.
Don’t fall foul of an avoidable crisis.
Having a 360° Service contract will ensure that your machines are kept in good working order, extending their lifespan and providing quick, efficient repairs should breakdowns occur.
Imagine your essential infection control machinery being out of service on the day of a CQC inspection…
It wouldn’t just be stressful – it could result in a devastating judgement on your overall quality of care. It simply isn’t worth the risk.
Make sure your staff are fully trained on infection control procedures.
There’s little point in investing in top-notch infection control machinery if your staff don’t use them properly; cut corners and lack of knowledge will be quickly picked up during the CQC inspector’s observation.
To help your staff provide the best possible care, it’s vital to make sure they are fully and regularly trained in good sanitation control procedures.
DDC can help, with training sessions in the use of infection control machinery. For peace of mind, it’s essential to keep records of this training accessible and up-to-date, as they could be requested during your inspection.
With these factors in mind, your facility will not only be ready for its CQC inspection, but your service users will be continuously kept safe from HCAIs.
Which is, of course, the best possible outcome.