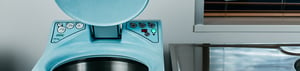
Why Is A Sluice Room Designed a Certain Way?
Sluice/dirty utility rooms are dedicated to the safe and efficient disposal of human waste and other potentially infectious material.
However, installing a bedpan washer or pulp macerator in a utility closet does not make it a sluice room.
Sluice/dirty utility rooms are far from glorified janitor closets, instead performing a vital role in the fight against infectious disease.
There is a common misconception that sluice/dirty utility rooms harbour infectious disease purely because that’s where the infectious material goes.
In fact a properly designed and equipped sluice/dirty utility room, when allied with diligently observed infection control policies, becomes a nexus of hygiene within a clinical setting.
The reason for this is entirely down to design. By this we don’t just mean what goes where – although this plays an important part – but the design of every single element that goes into that sluice/dirty utility room.
A sluice/dirty utility room should be designed and equipped to promote the best possible infection control practices which creates a safe environment for clinicians and patients alike. Take a look at our ultimate sluice room checklist to ensure you have all the necessary equipment to reduce the risk of infection outbreaks.
Materials
It is no coincidence that sluice rooms are built the way they are.
The objective is to create an environment where infectious material can be safely exposed of without either putting the clinician at risk or creating an environment for microbes to settle and grow.
Considering the heavy use most sluice/dirty utility rooms get on a day to day basis this is no easy feat and as much relies on the clinicians using the space correctly as it does the room itself.
Using materials such as stainless steel, anti-microbial coatings and non-porous flooring materials all help to prevent the spread of infectious disease.
But it’s not just the materials you use that are important. It’s the materials you don’t.
Low grade metals that oxidise (rust) in a damp environment can easily become a vector for harmful microbes.
Organic materials can absorb particulates and then be easily transmitted to other materials or to the human body with ease. Eliminating these from the sluice room – unless they are soiled garments in need of cleaning – prevents a possible means of transmission.
Technology
Having a sluice/dirty utility room isn’t enough. Until you install a means of disposal then you really do have little more than a janitor’s closet.
Our bedpan washers and pulp macerators are designed to quickly and safely dispose of infectious material.
Whilst singular focus, there is a great deal going on behind the scenes that both keeps the user safe and the disposal of infectious material as efficient as possible to minimise downtime and prevent delays.
This is achieved through innovations like hands free technology and anti-microbial coatings so clinicians never run the risk of coming into contact with potentially harmful microbes. The way in which the machines are manufactured also prevents anything harmful festering inside the machine itself.
Cleaning cycles are designed to ensure there is always a steady flow of water to the drains and macerators moisten, rather than soak, pulp utensils to prevent blockages and overflow.
Preventing major blockages alone represents a major safeguard as blockages have a major impact not just on the sluice room but on the facility as a whole.
The Room
A sluice/dirty utility room is an incredibly considered thing. Their location, what goes into them and what everything is made from matters a great deal.
The wrong grade of metal and a machine can rust. The wrong size of drainage pipe and the room can flood. The wrong location in your facility and you run the risk exposing patients and fellow clinicians unnecessarily to harmful material on your walk there. Not to mention the increased chances of spillages.
Equally, the layout of the room is important. Ultimately you want your clinicians and any reusable items they may be carrying to leave the sluice/dirty utility room clean.
As such you want them to follow a linear path around the room. Size of the room is undoubtedly a consideration but where possible clinicians should be travelling around the room rather than crisscrossing from one area to another. This circular flow prevents any stage of disposal and disinfection process from being accidentally missed.
The layout should allow for users to dispose of infectious materials and wash their hands before coming into contact or handling any other items with any items are handled. Storage areas for stocks of consumables, bedpans and bottles are also important.
Finally the design of the room also needs to consider lighting and ventilation. Lights need to be recessed and screened and ventilation should encourage laminar flow.
Do all of these things and you’ll have a sluice/dirty utility room that is well built, well designed and equipped with the best technology available to keep your clinicians and your patients safe.