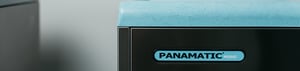
Understanding The Importance Of Weekly Washer Disinfector Tests
Balancing the bedpans (figuratively, of course) is a vital part of hospital ward and care home management.
When your bedpans are reusable, there’s an even greater need to stay on top of patient need, disinfection and recirculation; any break in the cycle could have catastrophic consequences.
If you’re using a washer disinfector for your reusable bedpan needs, you’ll be well aware of the benefits; they’re quick and easy to use and dramatically reduce the risk of infection. In the battle against HCAIs, they’re the weapon of choice for a wealth of healthcare institutions.
Ensuring that your washer disinfector has maximum uptime should, therefore, be a high priority for your estates management team.
Any length of time where a bedpan washer is unavailable can cause chaos; not having enough bedpans for patients to use, as well as infection risk from bedpans which have not been efficiently cleaned can start a downward spiral. Patient health and wellbeing, as well as clinical reputation, will be on the line; meanwhile, your budget could be stretched paper-thin by the cost of repairs and emergency measures, before the sanity of your staff is even mentioned.
For more information on how to avoid the most common bedpan washer faults that can cause downtime, read this article.
Weekly washer disinfector tests can help to prevent major breakdowns.
Easily performed in-house, a weekly test can ensure that your washer disinfector is in good working order, as well as providing early diagnosis of potential issues, before they become big enough to disrupt your critical operations.
By putting a record of your tests together, you can also adequately prepare for CQC inspections (where proof of your infection control strategy may be requested), as well as spotting any patterns in operational issues.
A weekly washer disinfector test checklist is quick and simple to perform.
Ideally, the checklist should include:
- A record of the maximum temperature reached
- The time taken to complete the cycle
- A check that spray arms and nozzles are rotating freely
- A check that door seals are in good condition
- Removal and cleaning of strainers and filters
- Confirmation that the machine contains enough detergent (and is topped up if necessary).
Staying on top of the weekly test results can help you to uncover any gradual declines in condition, as well as obvious maintenance issues.
Are cycles taking longer to complete? Door seals becoming damaged? More detergent being used than normal?
These could all be signs of a maintenance issue waiting to hit; and by knowing in advance, repair or inspection by a professional can be arranged in good time, before the machine becomes completely unavailable.
A planned preventative maintenance contract from DDC will help to ensure maximum uptime for your sluice room machinery, as well as saving time, cost and stress for your facility.
DDC have fully-trained engineers strategically located throughout the UK, cutting long waits for assistance and ensuring that the help you need is never far away.
Whether you’re dealing with a regular maintenance issue or an emergency repair, a 360° Service contract will ensure that you’re always protected and help you to keep costs under control. If you have sluice room machinery made by a different manufacturer, we can fully service and repair these, too – even if the model has since been discontinued. It’s the perfect all-round solution.
Infection control underlines any good standard of facility management. By testing your sluice room machinery regularly, as well as using a planned preventative maintenance contract, you will dramatically reduce the likelihood of an HCAI crisis which puts patients and clinicians at risk.