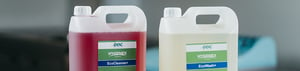
How To Avoid the Most Common Bedpan Washer Faults
Washer disinfectors provide much-needed security for hospitals and care homes which rely on reusable bedpans.
In the fight against HCAIs, reliable sanitation of reusable bedpans is absolutely essential. Human waste can carry a host of dangerous pathogens, and their ability to spread is heightened when items are shared; especially if poor infection control procedures are in place.
By using a bedpan washer disinfector, you may think that you’re protecting yourself in the best possible way – and if your washer works as intended, that’s often true. But what if your machine breaks down? Chances are, you couldn’t offer that same level of security to patients and clinicians without it.
If you keep your washer disinfector well-maintained, it’ll serve you with the uptime you need. But even if you stick to the recommended service intervals, you could come unstuck if the machine is damaged by users.
Many washer disinfectors experience faults that are entirely preventable. Here’s the top five, and how to avoid them.
1. Don’t Over-Fill the Washing Chamber
Your washer disinfector is designed to handle a specific number of items, which is made clear by the rack space inside. It’s imperative that you don’t overload it.
The rotators in the machine need to be free to move, or they will become damaged. Similarly, the machine can’t adequately clean more items than its intended capacity – so you could still be at risk of spreading infection, even after the wash cycle ends.
2. Use the Recommended Consumables
The chemicals that you put inside your washer disinfector must be fit for purpose, and suitable for that particular model.
Suitable cleaning agents are:
- Liquid (to facilitate accurate dispensing)
- Non-abrasive
- Low foaming
- Free rinsing
- Biodegradable
Detergents should not contain:
- Artificial colouring agents
- Perfumes
- Halides at an in-use concentration greater than 120 mg/L
- Fatty soaps, glycerine or lanolin
- Toxic residue.
In order to guarantee that your disinfectant won’t damage the machine, you should always use a product that the manufacturer specifically recommends. An incompatible disinfectant can cause serious problems, not limited to corrosion, embrittlement and swelling of plastics.
Even if an alternative consumable is cheaper – it simply isn’t worth the risk.
3. Only Wash the Advised Products
A bedpan washer disinfector is only designed to process reusable bedpans, urine bottles and commode pots. You shouldn’t attempt to sanitise any other items inside it.
Many materials can react negatively to the heat, chemicals or liquid used in washer disinfectors, as well as ultimately blocking the machine if the product starts to expand or fall apart.
4. Consider a Scale Inhibitor
Hard water areas can cause havoc for washer disinfectors, but with the right products, you can prevent the damage it threatens to cause.
Hard water can deposit a hard, mineral layer (limescale) when it’s heated or evaporated; when this settles on washer disinfector components, it can significantly reduce heat-transfer efficiency and can quickly lead to an increase in heating costs.
In addition, limescale deposits on the edges of spray nozzles will lessen their performance, leaving the washer disinfector unable to do its job to full capacity. In fact, even the efficiency of detergents and disinfectants can be hampered by hard water.
The solution? Be sure to use an appropriate scale inhibitor – such as Scalematic – to stop limescale from coating and damaging machine parts, or hindering your disinfectant.
5. Run Regular Tests
Many washer disinfector faults start with small indicators; but if you aren’t regularly testing your machine, you won’t notice them until the problem is much bigger.
Spot problems before they hit by testing your washer disinfector weekly. The following checklist is a good place to start:
- Record the maximum temperature reached
- Record the time taken to complete the cycle
- Check that spray arms and nozzles are rotating freely
- Check that door seals are in good condition
- Remove and clean strainers and filters
- Confirm that the machine contains enough detergent (and is topped up if necessary).
If you see a decline in performance from these records, it’s time to call a maintenance technician to diagnose the problem. As you’ve spotted the issue early, inconvenient machine inefficiency and downtime is likely to be mitigated.
Protect the efficiency of your washer disinfector with DDC’s 360° Care Cover.
Don’t leave your washer disinfector’s uptime to chance. With 360° Care Cover, your machine is protected from unforeseen maintenance issues, so patients needn’t be put at preventable risk.
With three levels of cover including a 5-year parts and labour warranty, staff training and machine commissioning, you can benefit from unparalleled protection against breakdowns – with no additional costs.
With the largest fleet of technicians in the UK, as well as the ability to service and maintain all brands of sluice room machinery, you needn’t fear the unexpected.